A new multi-functional material which can be used to purify water, as a recyclable construction material, and as a lightweight machine component for possible use in soft robotics, can also be moved remotely by a magnet.
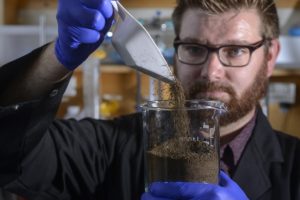
The new material that has been created and tested in the at Flinders University is made from magnetic iron particles and a sulfur-rich polymer, which combines elemental sulfur (a by-product of petroleum refining) and an unsaturated plant oil, such as canola oil.
A mixture of these substances is simply hot-pressed to make the key material, with the iron particles imparting the ability to move the material with a magnet.
The iron also allows the material to be heated very rapidly with microwaves. This enables curing into a desired solid shape within seconds.
This versatile new material is also recyclable, as it can be ground up and re-shaped multiple times.
The study – ‘‘ (2022) by Nicholas Lundquist, Yanting Yin, Maximilian Mann, Samuel Tonkin, Ashley Slattery, Gunther Andersson, Christopher Gibson and Justin Chalker – has been published in the journal Polymer Chemistry. DOI: 10.1039/D2PY00903J.
It marks another significant development from the team in the Chalker Research Lab, which continues to make important advances in green chemistry through creating new molecules and materials.
Lead author and Flinders University PhD Dr Nic Lundquist explains that the research team used the magnetic composite material in several applications. For instance, they used it to bind mercury in mine tailings, and then they retrieved the material (bound to mercury) with a magnet.
“This is a simple way to remove toxic metals from complex mixtures,” says Dr Lundquist.
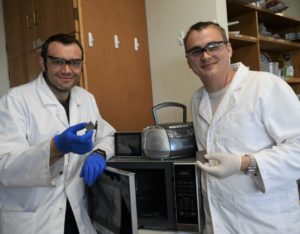
The magnetic-responsive material was also demonstrated to be an effective binder for new construction materials, charting new paths for converting waste into value-added products.
The team also fashioned a solenoid valve from the material, by rapidly shaping and curing the machine component in a microwave. The valve component was one-tenth of the mass of the original all-metal component.
“I’m very excited about the possible new applications of these polymers and can envision uptake in different fields, from environmental remediation to robotics,” says Dr Lundquist.
Matthew Flinders Professor of Chemistry Justin Chalker says the new research provides important additional evidence of the potential and versatility of sulfur-rich polymers.
“This study illustrates the expanding utility and reach of sulfur-rich polymers,” says Professor Chalker. “Heavy metal remediation, novel construction materials and light-weight and recyclable machine components were all made from this single, versatile material.”
Acknowledgements: This study received funding from the Australian Research Council (DP2001000900).